我們在
調(diào)節(jié)閥鑄鋼件的鑄造生產(chǎn)中,常會出現(xiàn)縮松和夾雜類缺陷,因此生產(chǎn)控制有一定的難度。本文將結(jié)合
閥門鑄鋼件的生產(chǎn)實際,主要分析不同種類夾雜和縮松缺陷的形成機制,提出工藝控制的技術(shù)思路和措施,為鑄鋼閥門的生產(chǎn)提供技術(shù)參考。
一、夾雜類缺陷
1、夾雜類缺陷的類型
通常所說的夾雜類缺陷,包括:砂、渣、雜三種。鑄鋼閥門經(jīng)常出現(xiàn)的夾雜類缺陷包括以下情況。
(1) 在一些鑄件的下型部位靠近芯子下面,加工時常常暴露出存在細小白點,位置在表層4~6mm的厚度內(nèi),若加工余量大則可去掉,若加工余量小,則需要現(xiàn)場焊補挽救,增大費用。
(2) 一些鑄件在靠近內(nèi)澆道附近有沖砂、結(jié)疤、粘砂等現(xiàn)象。
(3) 一些鑄件上表面局部處有較大面積的贓物(夾雜物),并常有渣孔、氣孔。
(4) 個別較大的鑄鋼件,上表面或側(cè)面上部出現(xiàn)印痕、皺紋,橘皮和麻坑也有發(fā)生,修補打磨工作量較大。以上是肉眼可見的宏觀缺陷。經(jīng)X射線探傷時,常常反映出細微的夾雜物很多,只是未超標,鑄件仍合格。為了獲得優(yōu)質(zhì)鑄件,提高內(nèi)在質(zhì)量,也需要對此類缺陷進行控制。
A、掉砂(砂眼)
內(nèi)因:鑄型的強度較低,局部緊實度不夠;或者水玻璃砂的CO2硬化效果不理想。
外因:澆注過程中流速過大、紊流,沖擊鑄型,或下芯合箱時掉砂。
(1) 鑄型強度與水玻璃加入量及CO2硬化的工藝有關(guān)。必要時可對硬化后的鑄型進行烘烤以提高強度。一般來說,水玻璃加入量為6.5%~7.5%是比較合適的。只是面砂(新砂)厚度不均,對吹氣要求較高,要均勻,深淺適中。
(2) 鑄型受到的流動沖擊,是因鋼液流速過大所引起??稍跈M澆道上增設阻流段,增大流動阻力,降低流動速度,在工藝設計時采用大孔出流理論計算澆注系統(tǒng)截面積,實現(xiàn)大流量、低流速、平穩(wěn)潔凈地充填。
(3) 下芯操作方面也應細致,防止可能的掉砂。
B、夾渣
夾渣(渣眼)———渣滓,屬外來非金屬夾雜物。
一次渣:鋼液熔煉和處理過程中生成的渣滓隨流進入型腔。大多屬于人工或澆注系統(tǒng)擋渣效果不理想所致。
二次渣:澆注過程中鋼液氧化形成的渣滓進入型腔。大多屬于內(nèi)澆道嚴重射流所致。
對鑄鋼來說,充填過程中金屬液和型腔中的氣體、造型材料相互作用,產(chǎn)生Al2O3、SiO2、MnO、FeO等組成復雜的二次渣滓(主要是硅質(zhì)玻璃基和剛玉X2Al2O3晶體),進入型腔后形成表面或內(nèi)部渣孔。
用鋁終脫氧,形成Al2O3,若粒徑小于5μm,其在10~30min內(nèi)難以聚集長大,達到肉眼可見的宏觀夾渣物浮出,只能彌散分布于鋼液中。實踐表明,濕型生產(chǎn)鑄鋼件,用鋁終脫氧,易在上表面或側(cè)面處形成夾渣。水玻璃CO2硬化砂,由于其中含有水分,在未烘干的情況下,也常出現(xiàn)夾渣缺陷。
C、夾雜物
包括內(nèi)生的氧化物、硫化物,如FeO、MnO、MnS等,至凝固后期偏析所致(偏析夾雜物),本來其體積很小,處于凝固過程中浮不出來,就會成為微小夾雜質(zhì)點。一般情況下不作為缺陷處理。
2、成因分析
以上問題,集中反映出鑄件的澆注工藝不甚合理[5]。主要問題是內(nèi)澆道截面積偏小,導致澆注速度慢,充型時間偏長;同時,內(nèi)澆道的出流速度又可能偏大,射流嚴重,卷入氣體,或形成紊流,引起鋼液進入型腔的過程中發(fā)生氧化,生成較多的二次夾雜物(如MnO、SiO2、Al2O3、FeO等)。這些夾雜物的分布可能有3種情況:一部分浮在液面上形成氧化膜,隨流上升,被上升的鋼液沖破分向四周,隨即粘附在型腔表面,形成流痕、皺紋。一部分比較分散細小的夾雜物,本身在鋼液中上浮速度小,在澆注速度也小的情況下,鋼液由于溫度降低較多,粘度增大,使這些氧化夾雜上浮到一定高度處停留下來,特別容易粘附在芯子的下表面處,故此處機加工后比較明顯。也不排除鑄件上表面處同樣存在這類白點。一部分夾雜物上浮到鑄件表面處形成表面渣孔、氣孔,清砂后肉眼看不見,噴丸后出現(xiàn)坑洞、麻點。
由于內(nèi)澆道出流速度大,沖壞型芯,帶起砂團,或沖刷掉一些小砂粒,造成砂眼、白點甚或夾砂結(jié)疤缺陷。
采用翻轉(zhuǎn)式澆包澆注時,扒渣不凈,擋渣不嚴,鋼液上面的贓物隨流進入型腔,而澆注系統(tǒng)本身的撇渣功能又不強,贓物上浮至鑄件頂部,若不能進入冒口,則留下玻璃質(zhì)渣滓,噴丸后出現(xiàn)凹坑、麻點等。
集中的原因是內(nèi)澆道截面積偏小,導致出流速度過大,氧化嚴重;且澆注速度偏小,澆注時間長,鋼液降溫太多,粘度增大,非金屬夾雜物、砂粒、渣滓等未能及時上浮進入冒口。
3、預防措施
A、改進澆注系統(tǒng)設計和澆注工藝
澆注系統(tǒng)截面尺寸的設計,應保證實現(xiàn)大流量低流速平穩(wěn)潔凈地充填。
(1) 加大澆注系統(tǒng)各單元的過流截面積,特別是內(nèi)澆道的截面積,以求減小出流速度,實現(xiàn)平穩(wěn)充填,避免鋼液的氧化。澆注系統(tǒng)設計時,若按傳統(tǒng)的奧藏公式計算,一般偏小20%~25%。如果澆注重量中不包括澆注系統(tǒng)的重量,則計算誤差更大(因為鑄鋼件的工藝出品率低),可在此基礎上加大。為了提高計算精度,建議按照大孔出流澆注系統(tǒng)設計方法計算澆注系統(tǒng)截面積,結(jié)果比較準確合理,同時注意按澆注效果及時調(diào)整修正。
(2) 采用開放式澆注系統(tǒng),特別是一些較大的鑄件。使內(nèi)澆道截面積大于前面的2個單元。只有內(nèi)澆道截面積大,才能降低出流速度,實現(xiàn)平穩(wěn)潔凈地充填,以防止噴射、紊流、氧化、沖砂及內(nèi)澆道局部過熱等。如果采用底注式或中注式澆注系統(tǒng),應特別強調(diào)開放。因為底注、中注方式,直澆道壓頭高,一開始出流速度就很大。
(3) 底注或中注,應保證快速澆注。因為底注、中注充型完畢后,進入冒口的鋼液經(jīng)歷了較長的路程和時間,溫度最低,而鑄件下部由于有剛進來的高溫鋼液,溫度高,在鑄件高度方向上,形成反的或倒的溫度梯度,既不利于夾雜物上浮進入冒口,也不利于頂部冒口由下而上順序凝固補縮。快澆,充型時間短,有利于減小底注和中注的鑄件上下溫差,有利于夾雜物上浮進入冒口。
(4) 加強澆注系統(tǒng)的擋渣功能
澆注系統(tǒng)中有擋渣功能的主要組元是橫澆道,橫澆道截面積大,流速減慢,渣輕易上?。M澆道頂面上的玻璃狀渣滓)。據(jù)此,橫澆道截面積的設計很重要,條件是橫澆道要充滿流動。
采用漏包底注具有良好的擋渣效果。
但不是所有渣滓都能擋住,渣滓越小上浮速度越慢,易隨流進入型腔,形成渣孔。
(5) 要求澆注工一定要保證滿流澆注。即認流要快,澆注系統(tǒng)一定要充滿(主要指直澆道)。對每種鑄件,工藝上按其澆注重量(包括澆冒口)確定合理的澆注時間,并力求達到,誤差不能太大。加大澆口杯,使?jié)沧⑦^程中澆口杯的鋼液始終保持一定高度,在即將澆滿時提前收包,把握住不在澆口杯內(nèi)留存鋼液。
快澆易出現(xiàn)抬箱跑火,應卡緊上下箱,糊好合箱面,防止抬箱跑火。同時,排氣道的總面積(主要是明冒口和出氣孔)應不小于直澆道總面積,避免快澆時型腔內(nèi)憋氣或嗆火。
綜上所述,改進澆注系統(tǒng)設計和澆注工藝,對鑄件的表面質(zhì)量和內(nèi)部致密度的提高,有綜合效應。
B、凈化鋼液
(1) 采用過濾技術(shù)
采用泡蜂窩孔陶瓷過濾器。該品用Al2O3(剛玉)等耐火材料,磷酸二氫鋁作粘結(jié)劑,和泡體等混合于1540℃燒結(jié)而成,鑄鐵、鑄鋼都能應用,也有用陶瓷孔過濾片的。
(2) 鋼液要精煉,脫氧要徹底,保證爐料無銹少銹,出爐后靜置(?5min)扒渣。從鑄件表面發(fā)生皺皮來看,說明澆注溫度可能偏低,鋼液氧化比較嚴重。所以堅持常測溫,保證所需的澆注溫度是重要的工藝控制因素之一。
二、縮松(顯微縮松)
1、縮松的形成和部位
生產(chǎn)中常常發(fā)現(xiàn),一些閥門鑄件打壓時有滲漏,如閥門的側(cè)法蘭下部與閥體連接處有縮松;有的閥門雖不滲漏,但X射線探傷檢查顯微縮松出現(xiàn)較多,達不到優(yōu)質(zhì)品等級。從不同企業(yè)鑄鋼閥門的生產(chǎn)情況整體來看,縮松的問題不是十分嚴重,或者說不很普遍。因為閥門鑄鋼件在工藝設計上較多的強調(diào)補縮,安放的冒口尺寸大且數(shù)量多,通常一個中小型閥門,在3個法蘭處設置3~4個冒口,鑄件中部頂面上設置1個冒口,共4~5個冒口,還要使用金屬補貼,加上保溫冒口套的作用,補縮效果應該是很不錯的,只是工藝出品率偏低,約50%~55%。
針對閥門鑄鋼件的特殊結(jié)構(gòu)和既定澆注位置,常在遠離冒口(垂直或水平方向)的件壁中心發(fā)現(xiàn)顯微縮松(X射線探傷)。
(1) 閥門鑄件的本體壁厚比較均勻,而冒口多設置在孔口法蘭加工面處,鑄件本體上一般很少設置冒口,也很少加金屬補貼(本體不加工),這樣會導致冒口的有效補縮距離不夠,易在件壁形成中心縮松。個別尺寸較大的薄壁閥門中,縮松出現(xiàn)較多。
(2) 鑄件拐角等局部小熱節(jié)處,凝固比周圍稍慢,未能實現(xiàn)順序凝固補縮,也易發(fā)生微小的縮松。縮松的出現(xiàn),仍然應該歸結(jié)到補縮工藝設計不到位,集中反映為冒口補縮距離不夠?;蛘呤敲翱谥腥鄙傺a縮鋼液,或者是輸送距離遠,未能形成良好的楔形補縮通道。
縮松形成的空洞,其總?cè)莘e是很小的,所需補縮鋼液的量也很小,但凝固后期補縮液在枝晶間流動,阻力很大,基本上為滲流,故冒口補縮的工藝措施往往事倍功半,即使加大冒口尺寸也往往難于濟事。
2、防止縮松缺陷的工藝措施
工藝改進的思路是,從縮松發(fā)生部位起,采取工藝措施,保證朝向冒口的形補縮通道暢通。
對局部出現(xiàn)的縮松(或內(nèi)部縮孔),可采取具體措施加以解決。
(1) 若法蘭底部(下箱)距頂冒口太遠,頂冒口的垂直補縮距離不夠,可以適當加大冒口,延長補貼,或加冷鐵于縮松發(fā)生處。
(2) 對靠近冒口處或兩冒口之間很小范圍內(nèi)出現(xiàn)的縮松,最好采取冷鐵來控制。使用冷鐵時,需要找準縮松發(fā)生的位置安放。
(3) 增大冒口有效補縮距離。在一般情況下,冒口有效補縮距離L=4.5T(T為鑄件壁厚),垂直補縮方向上L可大些,圓筒鑄件平澆L可小些。
以閥門鑄件的法蘭頂冒口為例,若壁厚T=4cm,則冒口有效補縮距離L=4.5×4=18(cm)(假設有末端區(qū)),可能遠小于冒口到法蘭最底處的距離,雖然法蘭端面上冒口下部設有補貼,使補縮通道延長,但法蘭處有較大直徑的芯子,鋼液通過法蘭圓周拐彎到達底部,補縮距離遠,補縮液流動的阻力大,補縮不到是能理解的。在工藝實踐中,可把法蘭頂部的1個冒口改為2個冒口,設在法蘭頂部的兩側(cè),縮短補縮流動的距離,可以提高補縮效果。
也可在法蘭底部容易產(chǎn)生縮松處安放冷鐵,增大末端區(qū)。
建議采用成形保溫補貼(和保溫冒口套一樣,采用絕熱材料做成),保持冒口補縮通道暢通。保溫補貼的補縮效果好,可節(jié)約金屬液,減少加工量。保溫材料與保溫冒口套的相同,按鑄件形狀和尺寸制模成形,造型時埋入,見圖1。在薄壁大件上,冒口加冷鐵仍解決不了的縮松,可考慮在鑄件分型面上遠離法蘭冒口的鑄件突出部位設置側(cè)冒口(如圖2),對該區(qū)域凝固后期可能發(fā)生的縮松進行補縮,也有減輕中間頂冒口負擔的作用。
但生產(chǎn)中有時發(fā)現(xiàn),在兩個冒口之間(冒口本身距離較近)會發(fā)生縮松。這是2個冒口對該處產(chǎn)生熱干擾,加上形成的砂尖散熱不良,延長了該處的凝固時間所致;還有可能是兩個冒口通過該處互相流通(連通器的作用),使此處和冒口同步凝固,后期得不到補縮出現(xiàn)縮松。防止辦法:可在兩冒口之間加冷鐵,放在芯子上,不要直接放在兩冒口之間,以免對冒口發(fā)生反作用。冷鐵放在芯子上,激冷效果不變,但不要阻礙件壁的收縮。
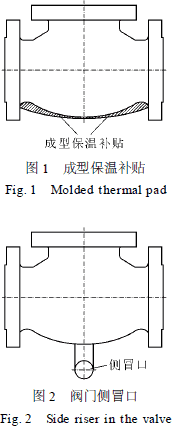
三、結(jié)論
1、為了防止和消除閥門鑄鋼件的縮松缺陷,應從優(yōu)化和強化補縮工藝設計入手,采用冒口、冷鐵和保溫補貼相結(jié)合的工藝思路,力求提高冒口補縮效果。
2、閥門鑄鋼件的夾雜類缺陷表現(xiàn)為砂眼、夾渣和夾雜物,形成原因主要歸結(jié)為澆注系統(tǒng)設計不合理,內(nèi)澆道截面積偏小,出流速度大,澆注時間長。建議工藝控制的思路和措施,應采用大孔出流理論設計澆注系統(tǒng),開放式截面比例,快速澆注,實現(xiàn)大流量低流速平穩(wěn)潔凈的充填;注意脫氧精煉效果,有效凈化鋼液;加強澆注系統(tǒng)的擋渣功能,包括使用過濾技術(shù)等。